High-capacity and at the same time fast-chargeable battery cells are considered a contradiction in terms. Nevertheless, the application industries expect high-energy lithium-ion cells that can be charged within a very short time.
The energy density of a cell can be increased by thicker and less porous electrodes. But the thicker the electrodes, the longer it takes the lithium ions to migrate from the cathode through the separator into the anode - and back again. A structure on the surface of the electrodes can accelerate this ion migration. These grooves form the so-called ion highways. Within these channels, the lithium ions can penetrate into the electrodes much faster. They then spread sideways into the active material. This idea is not new. So far, however, industrial cell production has lacked the right technology to structure the electrodes sufficiently deeply while fully preserving their functionality.
Electrode structuring promises to cut battery cell charging times by half or even a third. "Shorter charging times are primarily targeted in the automotive industry," says EAS Managing Director Michael Deutmeyer. "But fast-charging cells are also relevant wherever the battery-dependent service life of a machine is shorter than the working shift of its operators. This applies, for example, in mining or storage facilities with electric NRMM, the non-road machines and equipment."
The current solution approach is "laser structuring". Now that laser welding and laser cutting are firmly anchored in cell production, laser structuring could establish itself in the future as a third laser application in the production of large-format cylindrical cells. "A modern laser emits extremely short pulses, lasting less than a microsecond. Within this millionth of a second, the heat influence on the material next to the groove remains low and the material removal by the laser takes place precisely," says Michael Deutmeyer. "Laser technology brings electrode structuring into the realm of possibility." It would be particularly interesting for the series production of a gigafactory.
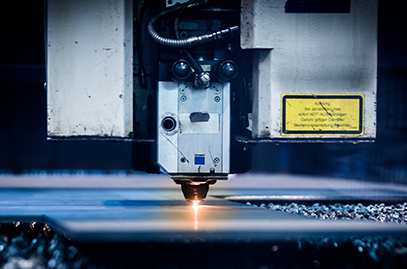
There are some challenges to the use of laser technology for electrode structuring. The active material that is removed from the electrode foil by the laser evaporates. The use of laser technology here requires a solution that captures and disposes of the condensed vapours in a way that is both environmentally and health-friendly. In addition, the laser structuring must always be adapted to the active material - thus to each new cell chemistry. This drives up the process development effort. On the other hand, laser structuring already saves time during the production of the cells. The filling of the cell with the electrolyte, an essential process in cell production, benefits from the structured electrodes, because the electrolyte does not have to penetrate completely through porous layers, but can flow along the ion highways. To enable this, the grooves extend to the edge of the electrodes.
In the overall view, laser structuring offers the chance to increase the energy content of the cells and at the same time to increase their charging speed. Additionally, it could extend their lifetime. "The performance of lithium-ion cells, like laser technology itself, will be able to improve significantly in the coming years," says Michael Deutmeyer. "We hope that the laser construction will also reduce the costs of the energy-dense and fast-charging cells.