More than two hundred thousand passenger and cargo aircraft cross the world's airspace every day. Apart from their maintenance, their propulsion systems are particularly expensive - both from an economic and an ecological point of view. The electrification of commercial aviation promises cost-efficient solutions and significant emission reductions through the introduction of new propulsion concepts and the associated efficiency improvements. It also enables new safety precautions in the air. EAS Managing Director Michael Deutmeyer highlights the challenges and opportunities of electric flying:
Cost reduction through electric propulsion systems
Commercial fixed-wing aircraft are in continuous operation. The permanent and safe use of these aircraft requires a constant supply of energy as well as short and strictly observed maintenance intervals. Operating costs thus represent the decisive cost factor of conventional flying. "Kerosene will be taxed ever more heavily in the coming years and the already high energy costs will thus rise significantly," says Michael Deutmeyer. "The main maintenance cost drivers are the thermal drive motors and the hydraulic and fluid systems. Electric motors, on the other hand, are enormously reliable and cheap to buy." The fully or partially electrified propulsion of aircraft reduces the maintenance effort and consumes significantly less energy in operation. This can be achieved on smaller aircraft, for example, by using electric drive motors, or on larger aircraft by using batteries for independent power supply on the ground. Another possibility is an integrated electric motor in the nose landing gear, which allows the aircraft to drive independently to the gate or runway with the main engines switched off.
Range through energy-efficient hybrid systems
Purely electric flying is conceivable in the foreseeable future for short-haul flights in passenger aircraft with thirty to fifty seats. These battery-electric aircraft require little special infrastructure and can be integrated into current air traffic with little operational adjustment. Battery charging containers at the gates allow fast charging independent of the airport power grid. To serve meaningful routes that do not have a direct land connection, for example, ranges of three to five hundred kilometres are required. "This is purely battery-electric feasible and also a competitive alternative in comparison with other means of transport. The gravimetric energy density must reach about 350 to 450 watt-hours per kilogram," says Michael Deutmeyer. "But I wouldn't separate classical and electric propulsion systems so strictly for flying. With the intelligent use of a so-called 'range extender', efficient flying with a long range is easy, at least in technical terms." The idea is to use a hybrid system - depending on the size of the aircraft and the engine technology used. Either a thermal engine drives a generator that generates electricity for the electric drive motor in addition to the battery, or the thermal engine and the electric engine complement each other in parallel and directly drive the so-called propulsor, for example the propeller or turbine wheel. Both variants extend the possible flight distance by several hundred kilometres in contrast to purely electric propulsion.
Safety through redundant engine concepts
Beyond the cost savings, electric flying brings with it the prospect of new safety standards. Electric engines are small and light. They can be installed several times in the aircraft. Should a propulsion system fail, it could be directly replaced by a twin. A range extender would also be available as an additional energy source.
For safety in the air, a safe, powerful and aviation-grade battery system with appropriate cell technology is crucial. The common cell chemistry for high-energy applications is currently based on nickel. "We are able to safely install high-nickel cathodes in a cylindrical cell, for example by working with a high-pressure electrolyte that immediately evaporates when the cell is opened," says Michael Deutmeyer. "But there are also promising approaches for lithium-sulphur cathodes. Sulphur is light, has a good gravimetric energy density and brings a good voltage. Sulphur cathodes could be the next evolutionary step in electric flight because it is an extremely safe cell chemistry, similar to LFP which is too heavy for aviation." In principle, cylindrical cell design is the cell format of choice wherever safety is a critical issue. Round cells withstand high internal pressure, dissipate heat optimally, are fast-charging and enable simple battery pack assembly. The high-performance round cell designs with good electrical and thermal connection as well as the safe propagation-avoiding behaviour, which are already part of the EAS development portfolio, are thus suitable for the beginning of electric flight.
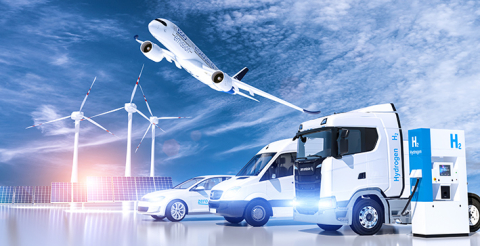
Weight reduction through innovative bipolar batteries
To electrify commercial aviation beyond individual smaller aircraft on short flight routes, further battery technology developments are required. Two essential aspects here are lightweight high-performance battery systems and their charging infrastructure.
"One solution approach for flight-optimised battery systems of the future could be bipolar batteries," says Michael Deutmeyer. "They promise a higher energy density for more range." The concept of a bipolar battery is reminiscent of cells with stacked electrodes, such as pouch cells. However - in that the anode always lies directly on the cathode - it consists of already interconnected sheets of active material based on an electrically conductive polymer. This eliminates the mechanically complex serial connection of the individual cells within a battery pack. "With a bipolar battery, we achieve an equivalent for battery systems that weighs only half as much. This would be a real breakthrough for electric flying," says Michael Deutmeyer. "We have the basic prerequisite for the production of bipolar batteries with our special EAS extrusion technology. It allows forward-looking bipolar concepts with extremely high specific energy. We have already successfully completed the first preliminary developments for a bipolar battery and are discussing the further development of this technology with potential partners and users. In the long term, lithium-ion technology will lead to bipolar battery systems. In the second or third generation, we consider energy densities of 500 watt-hours per kilogram at pack level to be possible."
A greater challenge for the overarching electrification of flight is the harmonised charging infrastructure. "Hardly any industry is as harmonised worldwide as aviation," says Michael Deutmeyer. "Every pilot must be able to land and communicate everywhere. Therefore, the language is the same everywhere - just like the signs, the fuels and all other specifics of aviation. Changing this globally is a lengthy process. The charging infrastructure must be introduced in a harmonised manner worldwide. We need the same voltage, the same plugs and the same software communication everywhere. Even if you start with the harmonised development of the charging infrastructure in Germany, it is a long way. However, this is precisely where EAS sees an opportunity that will lead to the development of a new market for standardised aircraft charging systems.
Climate protection through electrified aviation
Today's global air traffic contributes significantly to global warming. Although aviation's share of global CO2 emissions is currently only about three and a half percent - and rising sharply - nitrogen oxides emitted at high altitudes and the formation of contrails are also responsible for climate-damaging greenhouse gases. In addition, nitrogen oxides emitted near the ground are not harmful to the climate but to health. "Thus, the electrification of aviation has a significant effect on climate and environmental protection," says Michael Deutmeyer. "It also significantly reduces noise pollution, which is also a harmful environmental impact."
But how long will it be before electric flying is lived as naturally as travelling in an electric car is today? "It will take another five to ten years before the first prototypes can even enter long-term testing. Development cycles in aviation are long," says Michael Deutmeyer. "Cell and battery development also has a lot to do. So far, it has focused on the automotive sector, but now it should also take on aviation. The developments that have been made cannot be transferred one-to-one. It takes specialisation to master the new requirements and environmental conditions, such as a temperature difference of one hundred degrees, at system level. It can be done, but it needs attention and time. A big advantage in the electrification of aviation is that the routes follow clear patterns. These clear cycles help optimise the propulsion and battery systems."
Expectations for further developments within battery technology are naturally limited. "Optimised e-aircraft can certainly still achieve fifty to one hundred per cent better ranges under good conditions. After that, optimisation will be more concerned with concomitant issues," says Michael Deutmeyer. "How cheaply and intelligently can I produce? How climate-neutral can I make the range extender? How can I recycle the raw materials, how well do I implement the circular economy? It will then be a question of what cycle numbers the batteries will achieve; how durable they are and how they can save further costs. But if electric flying has actually become established at that point, that will already be an incredible revolution."