Die Anforderungen an neue Batterien steigen fortwährend, insbesondere an ihre Energiedichte. Darüber hinaus sollen sie leicht, robust, sicher, nachhaltig und kosteneffizient in der seriellen Fertigung sein. Möglich wird dies in einem komplexen Zusammenspiel aus mechanischem Design, elektrotechnischer Auslegung und abgestimmter Software. Dr. Stephan Horras, Leiter der Batterieentwicklung von EAS Batteries, hat vier Fragen zu den Möglichkeiten moderner Batterieentwicklung beantwortet:
Worin liegen die Kernherausforderungen einer kundenspezifischen Batterieentwicklung?
„Jede Batterie hat ihre eigenen Anforderungen. Sie setzen sich aus der geplanten Anwendung, regulatorischen Auflagen, der Verfügbarkeit passender Komponenten und den vom Auftraggeber gewünschten Eigenschaften zusammen. All diese Parameter werden in einem Spezifikationsdokument, dem sogenannten Lastenheft, gesammelt und auf Machbarkeit überprüft. Der wichtigste Punkt ist hierbei, eine lieferbare Zelle mit der passenden Energiedichte zu finden, die wir innerhalb der vorgegebenen Maße des geplanten Batteriesystems anordnen und verschalten können. Wenn es keine geeignete Lösung auf dem Markt gibt, müssen wir die Anforderungen an die Zell- und damit auch an die Batterieeigenschaften abändern. Alternativ dazu können wir anbieten, eine neue Zelle zu entwickeln. Sobald eine geeignete Zelle gefunden ist, schauen wir, welchen TRL, also welchen technology readiness level, der Kunde für sein System braucht. Dient die Batterie nur einer Machbarkeitsdemonstration, reicht ein elektrisches Modell, das keine speziellen Normen erfüllen muss. Geht es um eine Batterie in Serienreife, beziehen wir die erforderlichen Zertifizierungen und Tests in die Entwicklung ein. In den anwendungsspezifischen Normen verbirgt sich die eigentliche technische Herausforderung für uns, da sie meist ein enges Korsett bilden. Der größte Leistungsdruck liegt allerdings darin, die Batteriesysteme zu immer günstigeren Fertigungskosten zu entwickeln.“
Welche Batterieeigenschaften steuert das mechanische Design?
„Im Wesentlichen muss das mechanische Design sicherstellen, dass die Zellen und die Elektrik im Gehäuse der Batterie sicher befestigt sind. Komponenten wie Schrauben oder Muttern dürfen sich nicht lösen, auch nicht bei einer Schock- oder Vibrationsbelastung. Die Spannbreite zwischen den verschiedenen Applikationen ist groß. Bei normalem Betriebszustand auf einem Schiff ist die Batterie permanenten kleinen Vibrationen ausgesetzt. Bei den verschiedenen Zündungsphasen einer Raumfahrt-Rakete muss sie hingegen explosiven Schocks mit bis zu zehntausend g, also der zehntausendfachen Erdschwerebeschleunigung, standhalten. Auch das Gehäuse muss diese Belastungen aushalten und gegebenenfalls weitere Eigenschaften mit sich bringen – wie zum Beispiel Dichtigkeit gegen Wasser oder Staub. Daher muss das mechanische Design auch die thermische Auslegung berücksichtigen. Ist das Gehäuse dicht, kann die beim Laden und Entladen entstehende Wärme nicht über eine Lüftung abgeführt werden. In diesem Fall braucht die Batterie eine Flüssigkeitskühlung. Für Auftraggeber besonders relevant sind auch die aus dem mechanischen Design entstehenden Prozesse der Fertigung. Hier wächst der Anspruch, dass die Batterien in der Serienproduktion mit möglichst wenigen Arbeitsschritten und möglichst automatisierbar gefertigt werden können. Somit steuern wir mit dem mechanischen Design die Robustheit der Batteriesysteme sowie ihre Kosteneffizienz unter Berücksichtigung der Gewichtsvorgaben. Darüber hinaus haben wir hier auch die stärksten Hebel, um die Batterie nachhaltig zu gestalten. Zum Beispiel ist es für das Recycling wichtig, dass sich die Batterie am Ende ihres Lebenszyklus wieder in ihre Einzelteile zerlegen lässt. Hier gilt es, möglichst keine Komponenten zu verkleben.“
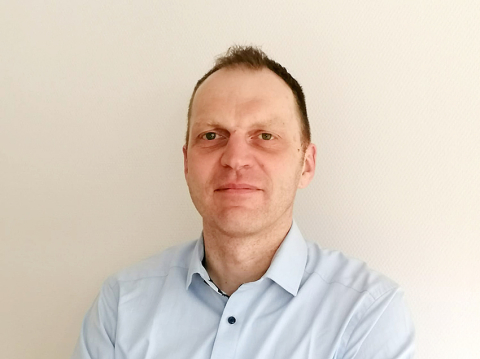
Welchen Einfluss hat die Elektrik auf die Merkmale der Batterie?
„Das Batteriemanagementsystem (BMS) ist die Kernkomponente der Elektrik. An die elektronische Leiterplatte werden die sogenannten Schütze und verschiedene Sensoren angeschlossen. Die Sensoren ermitteln wie hoch der Ladestrom, die Spannungen und die Temperaturen sind. Die Schütze öffnen und schließen bei Bedarf wie elektronische Schalter. Hier sitzt auch der sogenannte Isolationswächter, der die Batterie beim Unterschreiten der minimalen Isolationsschwelle abschaltet. Alle diese Komponenten dienen der Batteriesicherheit. Je nach Anforderung an den Sicherheitslevel der Batterie verbauen wir zusätzliche Sicherungen, die bei Überstrom auslösen. Zudem haben wir in der Elektrik aufgrund der Vielzahl kleinteiliger Komponenten die detailreichsten Möglichkeiten, die Kosteneffizienz der Batterie zu optimieren. Oftmals findet sich im Markt eine breite Preisspanne für vergleichbare Bauteile. Zudem kommt es darauf an, die elektrischen Anforderungen immer ideal zu treffen und keine überdimensionierten Elemente zu verbauen. Das wiederum wirkt sich auch auf das Gewicht der Batterie aus. Wir stimmen die einzelnen Komponenten so aufeinander ab, dass sie im Gesamtbild das Optimum der gewünschten Eigenschaften erreichen.“
Welche Funktion erfüllt die Software eines Batteriesystems?
„Wenn wir über die Software eines Batteriesystems sprechen, meinen wir im Wesentlichen die Software des Batteriemanagementsystems. Das BMS dient vorrangig der Sicherheit der Batterie, da es ihre Zellen überwacht und unterschiedliche Ladezustände ausgleicht. Je genauer wir den Algorithmus der Software an die Zelle anpassen, umso präziser, effizienter und sicherer arbeitet das BMS. Über eine Datenschnittstelle werden die Informationen auf eine grafische Benutzeroberfläche übertragen. Sie zeigt den Ladezustand und den sogenannten ‚state of health’, also den Gesundheitszustand, der Zellen an. Je nach Anforderung ist auch die Anzeige weiterer Parameter möglich, wie zum Beispiel die Temperatur der Zellen. In Zukunft wird ein BMS auch wertvolle Daten für eine nachhaltigere Nutzung der Batterie liefern können.“
Lesen Sie mehr über Batteriemanagementsysteme der Zukunft – Chancen und Herausforderungen.