Whether as vacuum and mopping robots in the hotel industry or for the intralogistical delivery of goods in aircraft construction - automated guided vehicles (AGVs) have found their way into various industries. They either move automatically along predefined routes or travel autonomously with the help of sensors and can therefore move freely and dynamically. Their original purpose is to transport goods, but their development potential is diverse. EAS Market Development Manager Joachim Kopf answered four questions about mobile robots:
How is the market for automated guided vehicles developing?
"An annual growth rate of 15 per cent is predicted for the global market for mobile robotics. AGV technologies are being continuously developed. The reasons for this are obvious. Automated material flows enable optimised, efficient and safe intralogistics processes - they are free from operator influence and are now also increasingly affordable. In addition, AGVs solve the cross-industry shortage of skilled labour, at least in some areas. They can be used in all kinds of large warehouses, in industrial manufacturing or increasingly in medical facilities - wherever goods need to be transported over short distances on a small or large scale."
What requirements do AGVs place on their battery systems?
"In driverless electromobility, safety is the top priority. It usually takes place where people are present. And even if not, there are goods of high value in their immediate vicinity. This means increased safety requirements for the battery system. It must also be designed for high load fluctuations so that it can deliver high energy currents at short notice during the process of lifting or lowering the transported goods. Depending on the place of use, ambient temperatures can also play a major role, for example in refrigerated storage or when transporting goods through a steriliser. The battery system must of course be able to withstand these temperatures. In addition, service life and charging speed influence the cost efficiency of the battery system.
How does EAS solve the battery technology challenges in the development of AGVs?
"EAS designs the battery as an integral part of the driverless transport system. If we are involved in the development of an AGV right from the start, we can supply a battery that precisely meets the requirements of its future application. The battery management system (BMS) plays a key role here. It controls the communication between the AGV and its control system. The BMS also provides data on the charge and health status of the individual cells to ensure smooth operation. In addition, the EAS team is constantly improving both the performance and the properties of its cells through intensive research and development activities.
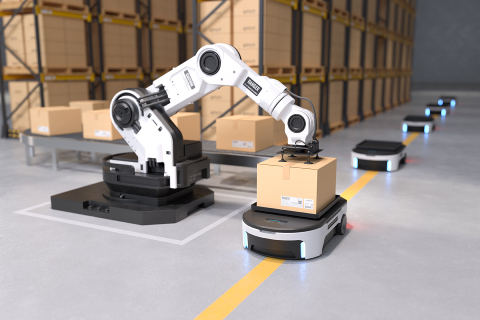
As specialists in the cell chemistry lithium iron phosphate (LFP), we also achieve the highest possible degree of safety in battery development. We optimise custom-specific battery systems for AVG to the required currents, temperatures, space conditions and their corresponding service life using our latest, partly patented, technologies. The type of cooling and the degree of insulation are also adapted precisely to the battery's area of application. Of course, it is also possible to fit battery systems into existing AGVs as part of a retrofit and get the best out of them within the given framework."
What trends will determine the future of AGVs and their applications?
"At the moment, we are thinking of intralogistics applications when we talk about driverless transport systems - the internal transport of materials, workpieces or waste on the company's own premises. But if we take this idea a step further, we find ourselves directly in the field of autonomous driving, for example when a driverless lorry brings its load from Stuttgart to Düsseldorf. These technologies are already being trialled on test routes. The requirements for the battery systems are basically similar here, just on a different scale. There will also be an increasing demand for driverless logistics, which will eventually lead to driverless passenger transport - AGVs and electric cars will merge.
Another trend in current intralogistics applications is the combination of transport and assembly - or other operational activities. Automated or even already autonomous transport systems provide the platform for so-called cobots, meaning industrial robots that collaboratively support human workers. The mobile robots can load or unload machines, perform automated assembly tasks or carry out measurements. They are also likely to be increasingly used for serving food in the catering industry or for serving meals in hospitals in order to compensate for the prevailing shortage of skilled workers."