The market for battery management systems (BMS) is on the verge of change. Hardly noticed by the user, these units of hardware and software are included in every battery. They monitor and control the cells contained in the battery. Their primary task is their safety function. They also provide information about the battery's state of charge and optimise it, if necessary, in a process known as "balancing". But these functions will no longer be sufficient in the future. And it will become more complex to implement them at all.
The demand for batteries with safe cell chemistry, such as lithium iron phosphate (LFP), is growing with the electrification of mobile machines as well as aviation and shipping. In parallel, the automotive industry is demanding increasingly fast-charging batteries with high energy density, whose properties require entirely new cell chemistries. But there is one constant: the BMS only has information about the current, temperature and voltage of the cells available as measured variables.
Cell chemistry: LFP and new active materials
The state of charge of battery cells with classic cell chemistries such as nickel-manganese-cobalt-oxide (NMC) or nickel-cobalt-aluminium-oxide (NCA) is almost proportional to the cell voltage. It can therefore be easily derived and displayed via BMS from this measured variable. With LFP, the situation is different, as the cell voltage in the range between twenty and eighty percent says hardly anything about the state of charge of the cell. "Here we need an algorithm, in other words a calculation by the software, which also takes into account the hysteresis behaviour characteristic of LFP cells," says Dr Stephan Horras, head of EAS battery development. "To do this, we first have to feed this algorithm with characteristic progressions of the state of charge of the LFP cell so that it can calculate a current state of charge at all. We have to collect the measurement data for this curve individually for each cell type in advance."
In general, a BMS works as well as it is aligned with the cell used. It is time-consuming, but effective, to measure the cells in detail and, through this characterisation, to collect data that can be used to optimise various algorithms, such as here for the "State of Charge" or also for the "State of Health" or the "State of Power".
This applies in particular to cells with novel cathode materials, for example the niobium oxide-based XNO® from Echion or the silicon nanowire technology SINANODE from OneD, which are currently being developed and tested. Research is also being conducted on the anode – moving away from the usual graphite towards more efficient alternative materials. However, any new combination of active materials on both the cathode and anode side will have an impact on the cell voltage and thus require adapted BMS algorithms to indicate the state of charge of a battery.
Parameters: Special functions and requirements of the upcoming EU regulation
The growing demands of the market are joined by regulatory requirements. For example, the draft EU regulation on "Batteries and Waste Batteries", which will replace the current directives in the coming years, stipulates that battery management systems for rechargeable industrial batteries must provide the user with detailed information on the ageing state and the expected service life of the battery. The exact parameters are defined in "Appendix VII" of the regulation. "This Appendix has what it takes," says Dr Stephan Horras. "We can already determine the expected service life with today's standards. But the parameters for determining the state of ageing do not reflect today's commercially available BMS by far.
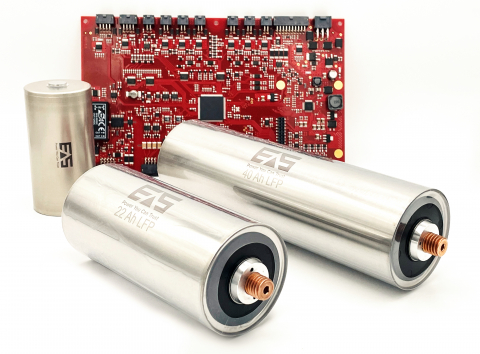
In future, the battery management systems will have to determine values during the ongoing operation of the cells, which today we only collect once before the cell is delivered." All the necessary data can still be determined by the three measured variables of voltage, current and temperature, but they must be collected and evaluated in much greater detail.
According to the current draft regulation, the remaining capacity, the total capacity loss, the remaining power capacity and the power loss, the remaining battery efficiency, the actual cooling requirement, the development of the self-discharge rate and the ohmic resistance or the electrochemical impedance are to be among the parameters that determine the ageing state of the batteries. The detailed characterisation of the cells will thus become even more important in the future in order to adapt the corresponding algorithms to the new requirements.
In addition to these general regulatory challenges for the battery management systems of the future, there are also always application-related safety standards and thus special functions that a BMS must fulfil. For example, components in the automotive sector must withstand temperatures of up to 125 degrees Celsius. In the maritime industry, depending on the application, batteries must shut down mechanically, meaning independently of the software, if a malfunction occurs at cell level. These are the highest safety requirements, which are already placed on modern battery management systems and are solved individually.
Future: Valuable data for more sustainable use
The BMS function of monitoring and controlling a battery remains a priority in terms of safety. But the new applications with optimised algorithms and the modernised legal framework bring valuable prerequisites for a more sustainable use of batteries. "From a technical point of view, the additional data we will obtain in the future are highly interesting," says Dr Stephan Horras. "We get exact figures that help us to maintain the battery in a targeted manner and thus to use it significantly longer. That is a key point in achieving the goal of sustainability. In addition, we would then be able to find out exactly whether the total capacity of the battery is declining in its 'natural' life cycle and could therefore use it with a clear conscience in a second life, thus in a new and less demanding application. All in all, the BMS makes the cell data much easier to interpret. This allows us to significantly prevent previously unforeseeable situations in which a battery could fail.”